We are Specialist in Thermofusion Pipe Welding
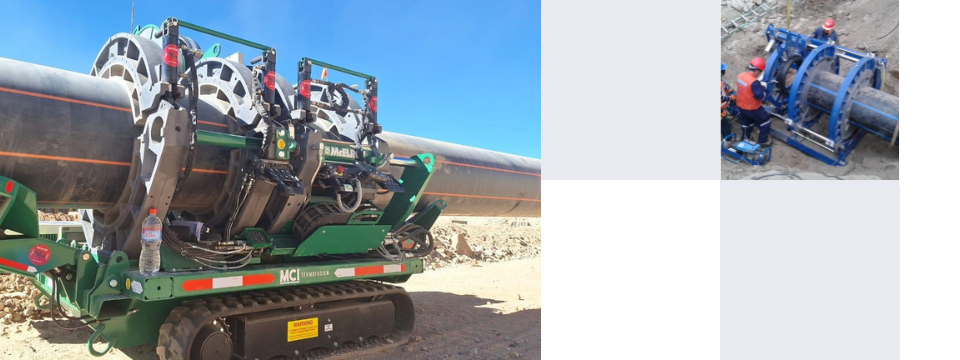
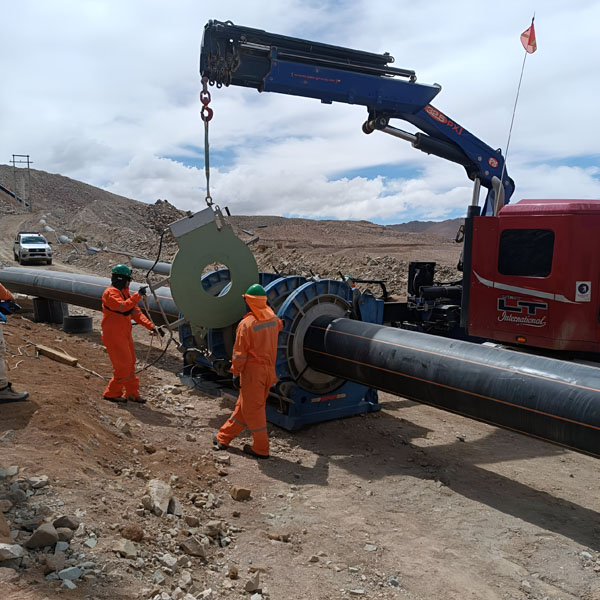
Pipe welding HDPE
In ROCCFLEX we have machinery to thermofuse HDPE pipes in diameters from 40 mm to 1200 mm. HDPE is the best existing polymer when it is necessary to conduct water, acid solutions, mineral treatment or other industrial fluids, especially over long distances, since there are no losses due to leaks or filtrations. In addition, projects developed in HDPE have a long useful life and do not require maintenance, since HDPE is a thermoplastic material with excellent mechanical properties, high chemical inertness, no polarity, does not absorb humidity, excellent performance as an odorless and physiologically inert electrical insulator.
Applications HDPE pipe welding
- HDPE pipe and fitting butt fusion, HDPE pipe electrofusion and fitting, and steel pipe arc welding.
- Conveyance of water for irrigation, acidic solutions, and tailings, with HDPE pipes.
- Conveyance of water and sewage in construction works with HDPE pipes.
- Conveyance of RILES and RISES for agro-industrial plants with HDPE pipes.
- Gas conveyance with HDPE pipes for high pressure.
- Solutions with special pieces for existing and operating conveyance systems.
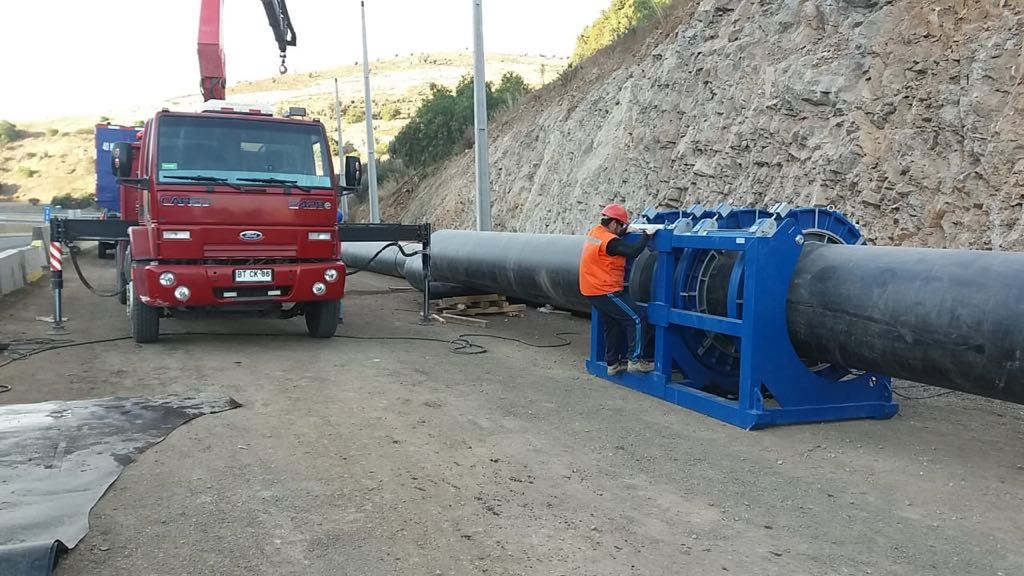
HDPE Pipe Welding Method: Butt Fusion
At ROCCFLEX, we specialize in HDPE pipe and fitting welding using butt fusion, an essential process to guarantee the integrity and durability of pipe installations in a variety of industrial and commercial environments. Our services are carried out on-site, where the pipes will be installed, taking into account environmental variables such as temperature and pressure to ensure optimal results. Additionally, we adhere to ASTM F 2620 A 2022 or DVS 2207 regulations, depending on customer specifications, to ensure the quality and safety of our processes.
Steps for Butt Fusion Welding of HDPE Pipes:
Pipe Preparation:
- Thorough cleaning to remove any residue.
- Precise adjustment of equipment jaws.
Facing of Edges:
- Careful equalization of pipe ends.
- Removal of burrs to ensure a perfect fit.
Heating for Fusion:
- Preheating of the heating plate and placement between the pipes.
- Gradual application of pressure and monitoring of the fusion process.
Cooling and Quality Control:
- Cooling according to established standards.
- Conducting comprehensive quality controls to verify the integrity of the joints.
This process is carried out with expert operators and certified machinery, complying with rigorous regulations to ensure optimal and long-lasting results.